Saiptech's Wire Mesh Coalescer
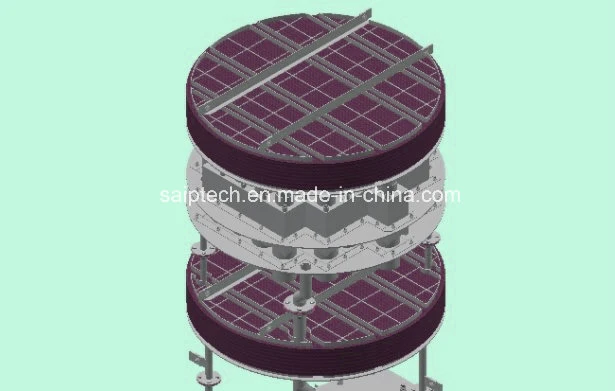
Liquid-Liquid Applications
Mixtures of immiscible liquids can generally be separated by a process of settling as a result of the density difference between the two phases. However gravitational settling becomes increasingly difficult as the droplet size of the dispersed phase decreases. The settling process can be enhanced considerably by passing the dispersion through a suitable coalescer pad.
Saiptech's Knitted Dual Media Mesh Pads are effective coalescers in both liquid-liquid and vapour-liquid service. Mesh pad style, face velocity and configuration will depend on the specific application.
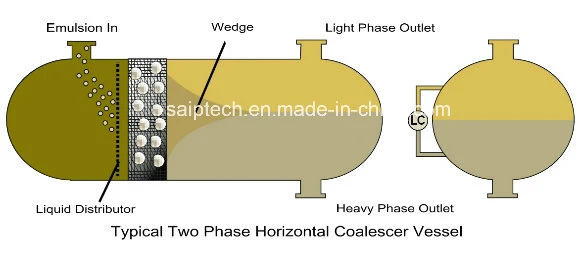
Liquid-liquid separator vessels are usually arranged horizontally as shown above. The coalescer pack is used to enhance the separation of liquid dispersions and consists of layers of composite materials chosen to suit service conditions. Generally a metallic wire monofilament is co-knitted with a fibre material which has a surface which is preferentially wetted by the dispersed phase. For hydrocarbon in water dispersions, a thermoplastic fibre is preferred and for water in hydrocarbon dispersion a specially treated glass fibre is used. It is therefore always important to know which is the dispersed phase in the mixture. Whilst the right choice of fibre material ensures maximum collection of the dispersed droplets, the effect of the difference in surface free energies of the monofilament wire and fibre materials in close proximity promotes droplet coalescence.
The Portfolio of Separator Internals
The comprehensive service from Saiptech
which can be tailored to your project requirements, including:
• process design
• feasibility studies
• detailed engineering
• equipment manufacture and supply
• installation
• trouble shooting
• de-bottlenecking
• revamp & capacity expansion
Applications
• Test Separators
• Production Separators
• Electrostatic Treaters
• Liquid/Liquid Coalescers
• Slug Catchers
• Cyclone Separators
• KO & FWKO Drums
• Flare Drums
• Compressor Scrubbers
• Pipeline Scrubbers
• Inlet Distributors
• Sand Removal Systems
Saiptech welcome the opportunity to assist our customers, including end users, EPC contractors and vessel fabricators, to select and customize from our standard range of separation internals to provide an optimized solution for any specific process and vessel configuration.
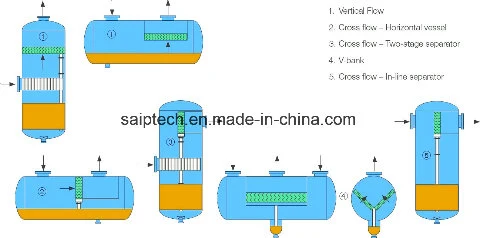
In an increasingly competitive business environment, we have developed a unique approach to providing added value and benefit to our customers by focusing on quality engineering rather than high volume manufacturing. our vessel internals, including distillation and absorption as well as separation equipment function as the vital organs of a process plant. Therefore, well engineered equipment is not only the key to long term profitability but intelligently engineered vessel internals may often result in lower overall capital costs.
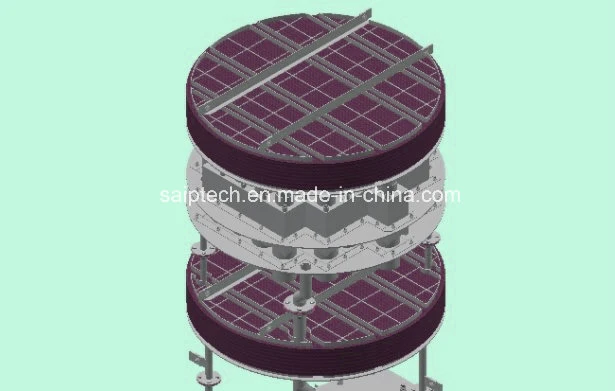
Liquid-Liquid Applications
Mixtures of immiscible liquids can generally be separated by a process of settling as a result of the density difference between the two phases. However gravitational settling becomes increasingly difficult as the droplet size of the dispersed phase decreases. The settling process can be enhanced considerably by passing the dispersion through a suitable coalescer pad.
Saiptech's Knitted Dual Media Mesh Pads are effective coalescers in both liquid-liquid and vapour-liquid service. Mesh pad style, face velocity and configuration will depend on the specific application.
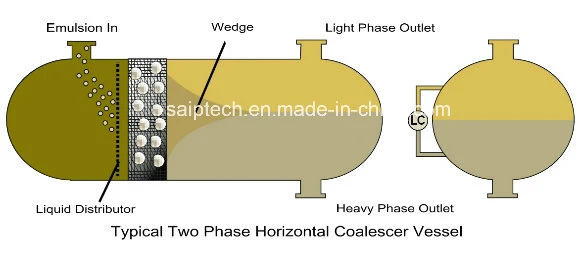
Liquid-liquid separator vessels are usually arranged horizontally as shown above. The coalescer pack is used to enhance the separation of liquid dispersions and consists of layers of composite materials chosen to suit service conditions. Generally a metallic wire monofilament is co-knitted with a fibre material which has a surface which is preferentially wetted by the dispersed phase. For hydrocarbon in water dispersions, a thermoplastic fibre is preferred and for water in hydrocarbon dispersion a specially treated glass fibre is used. It is therefore always important to know which is the dispersed phase in the mixture. Whilst the right choice of fibre material ensures maximum collection of the dispersed droplets, the effect of the difference in surface free energies of the monofilament wire and fibre materials in close proximity promotes droplet coalescence.
The Portfolio of Separator Internals
Inlet Devices | Distributors | Coalescers | Mist Eliminators | Others |
Deflectors | Perforated Baffles | Plate Packs | Wire Mesh | Desalter Grids |
Bifurcators | Slotted Baffles | Corrugated Packs | Vane Packs | Sand Jets |
Multi-Vane | Pipe Distributors | Matrix Packs | Axial Cyclones | Vortex Breakers |
Cyclone Defoamers | Wave Breakers | Mesh Coalescers | Multicyclones | Anti-Motion FPSO |
which can be tailored to your project requirements, including:
• process design
• feasibility studies
• detailed engineering
• equipment manufacture and supply
• installation
• trouble shooting
• de-bottlenecking
• revamp & capacity expansion
Applications
• Test Separators
• Production Separators
• Electrostatic Treaters
• Liquid/Liquid Coalescers
• Slug Catchers
• Cyclone Separators
• KO & FWKO Drums
• Flare Drums
• Compressor Scrubbers
• Pipeline Scrubbers
• Inlet Distributors
• Sand Removal Systems
Saiptech welcome the opportunity to assist our customers, including end users, EPC contractors and vessel fabricators, to select and customize from our standard range of separation internals to provide an optimized solution for any specific process and vessel configuration.
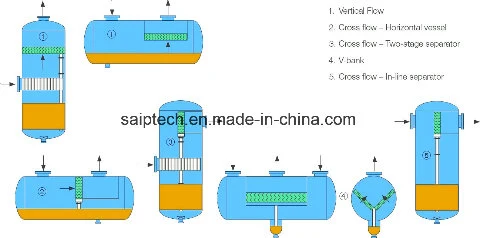
In an increasingly competitive business environment, we have developed a unique approach to providing added value and benefit to our customers by focusing on quality engineering rather than high volume manufacturing. our vessel internals, including distillation and absorption as well as separation equipment function as the vital organs of a process plant. Therefore, well engineered equipment is not only the key to long term profitability but intelligently engineered vessel internals may often result in lower overall capital costs.